Understanding of Industry Road crack codes
Note: 'damage code,' 'crack code,' and 'distress code' , 'deterioration code' are different expressions that convey the same meaning.
To gain a better understanding of road crack codes, it is important to know the different types of cracks that can occur in road pavements and their causes. This knowledge can aid in proper identification, assessment, and maintenance of pavement distresses.
Transverse Crack
Related code(s): APHCLN, CPHCLN
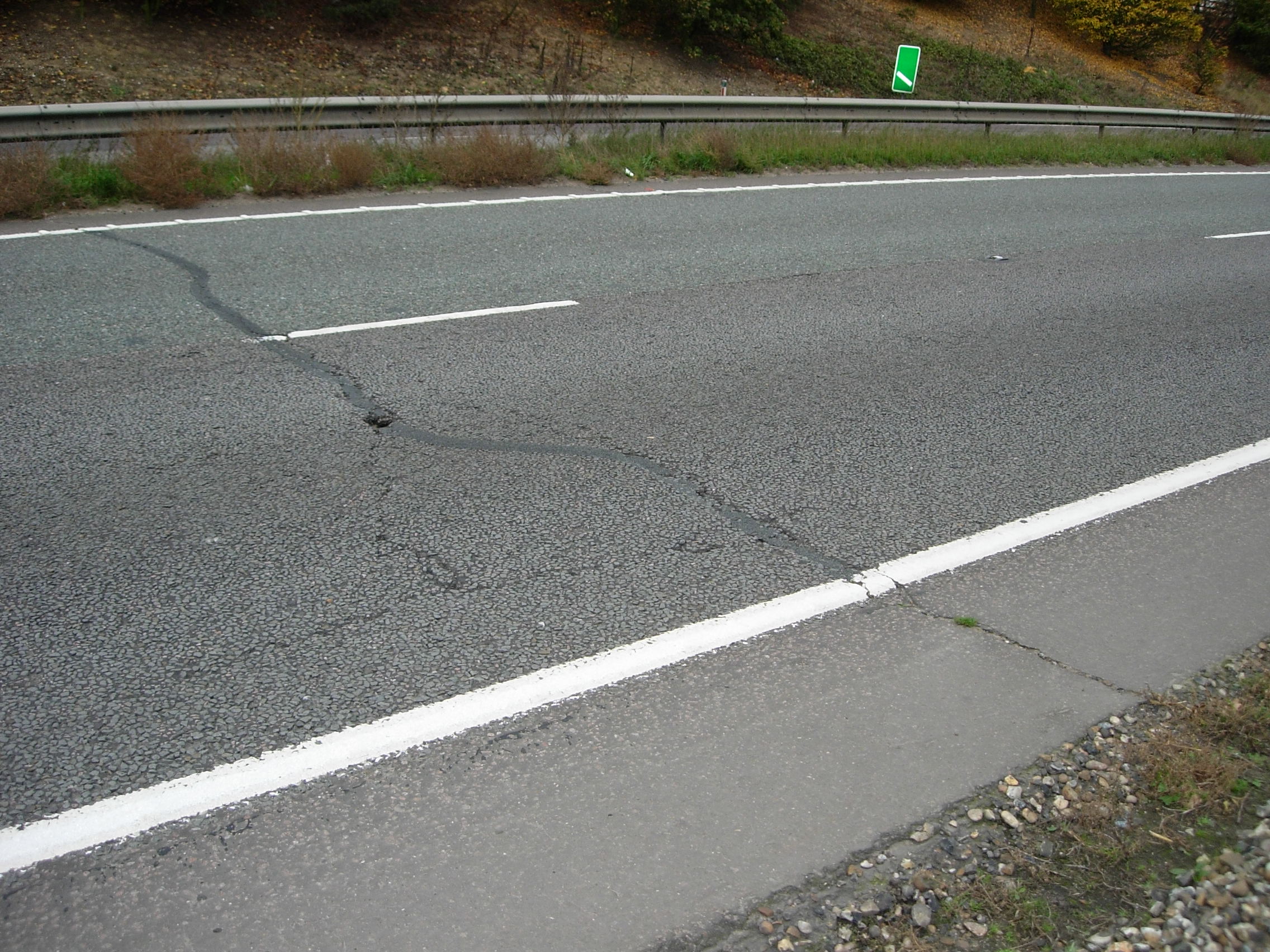
-
It is a crack that runs perpendicular or across the direction of travel. These cracks extend across the full width of the pavement, forming a roughly straight line across the travel lanes.
-
Transverse cracks can occur in both asphalt and concrete pavements and are typically caused by one or more of the following factors:
-
Thermal Movement: Significant temperature changes can cause the pavement material to contract or expand, leading to thermal stresses that result in transverse cracking if the movement is restrained.
-
Shrinkage: As concrete cures and dries or as asphalt pavements age, they tend to shrink. If this shrinkage is restrained, it can lead to the formation of transverse cracks.
-
Reflective Cracking: In the case of asphalt overlays on jointed concrete pavements, transverse cracks in the underlying concrete can propagate or "reflect" through the asphalt layer, resulting in transverse cracks on the surface.
-
Load-Associated Cracking: Repeated heavy traffic loads, especially at locations like intersections or stop lines, can cause fatigue cracking, which may manifest as transverse cracks.
-
Transverse cracks, if left unaddressed, can allow water infiltration and subsequent deterioration of the pavement structure. They can also create a rougher ride for vehicles and potentially lead to further cracking or spalling of the pavement surface. Regular maintenance, such as crack sealing or patching, is often required to prevent the progression of transverse cracks and extend the service life of the pavement.
Longitudinal Crack
Related code(s): APVCLN, CPVCLN
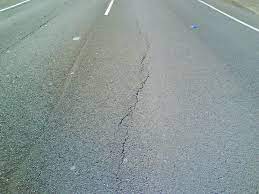
-
It refers to a crack that runs parallel to the centerline or direction of the road.
-
Longitudinal cracks in road pavements can occur due to various reasons:
-
Load-associated fatigue cracking: Repeated heavy traffic loads, especially along the wheel paths, can cause fatigue cracking in the pavement surface. These cracks typically start as hairline cracks and gradually widen over time.
-
Shrinkage cracking: As concrete or asphalt pavements cure and dry, they tend to shrink. If this shrinkage is restrained, it can lead to the formation of longitudinal cracks.
-
Thermal cracking: Extreme temperature changes can cause the pavement material to expand and contract, leading to longitudinal cracking if the movement is restrained.
-
Reflective cracking: In the case of asphalt overlays on concrete pavements, longitudinal cracks in the underlying concrete can propagate or "reflect" through the asphalt layer, resulting in longitudinal cracks on the surface.
-
Poor construction practices: Inadequate compaction, improper joint construction, or insufficient reinforcement can contribute to the development of longitudinal cracks in concrete or asphalt pavements.
-
Longitudinal cracks in road pavements are considered a structural distress and can compromise the pavement's performance and serviceability. They can allow water infiltration, which can further deteriorate the pavement structure and lead to potholes, spalling, or other forms of distress. Severe longitudinal cracking may require partial or full-depth repairs or even reconstruction of the affected pavement section.
Crocodile Crack (also known as an alligator crack or fatigue crack)
Related code(s): APTCAR, CPDCAR
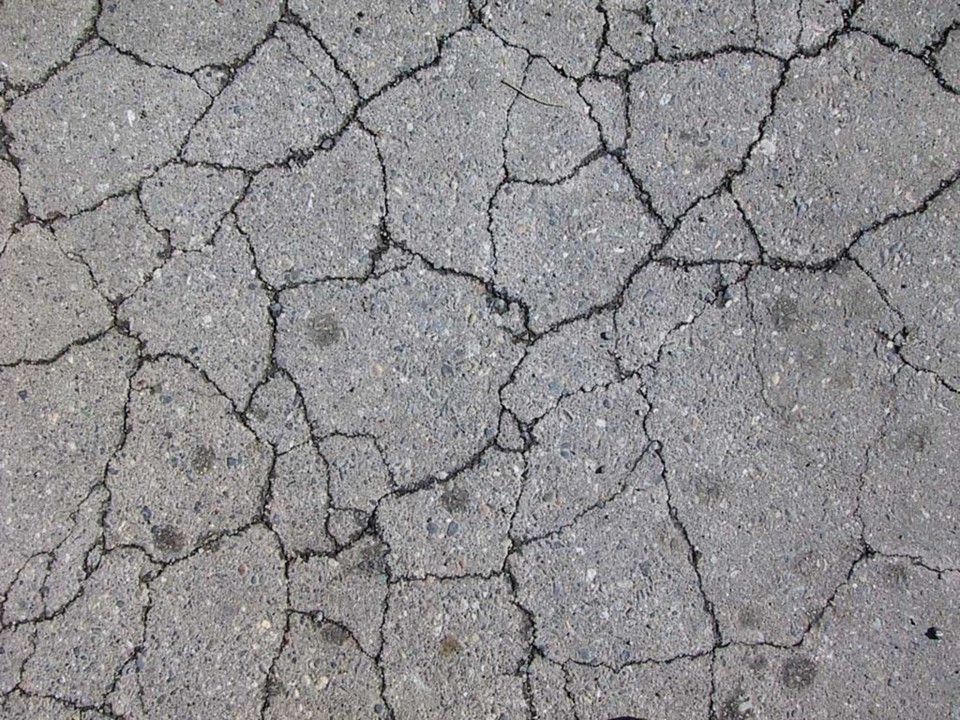
-
It is a type of structural distress that occurs in flexible pavements, typically asphalt concrete pavements.
-
Crocodile cracks are characterized by a pattern of interconnected cracks that resemble the skin of a crocodile or alligator. These cracks form an irregular, polygonal pattern on the pavement surface, and can be accompanied by localized upheaval or depression of the pavement.
-
Crocodile cracks are caused by fatigue failure of the asphalt concrete surface or the underlying layers due to repeated traffic loading. This type of cracking is particularly common in areas where the pavement experiences heavy traffic volumes and loads, such as intersections, bus stops, or truck lanes.
-
The formation of crocodile cracks typically follows a sequence:
-
Initial hairline cracks appear on the pavement surface, usually along the wheel paths.
-
With continued traffic loading, these cracks propagate and interconnect, forming a series of small, irregular blocks or polygons.
-
As the distress progresses, the blocks or polygons become more defined, and the pavement may experience upheaval or depression in the affected areas.
-
Crocodile cracks are considered a severe structural distress and indicate that the pavement has experienced significant fatigue damage. If left unaddressed, these cracks can lead to further deterioration, including pothole formation, and can compromise the structural integrity of the pavement.
-
In Pavement Management Systems, crocodile cracks are typically identified and rated based on their extent and severity. Depending on the level of distress, appropriate maintenance or rehabilitation strategies, such as partial or full-depth repairs, overlay, or reconstruction, may be recommended to address the issue and restore the pavement's serviceability.
Reflection Crack
Related code(s): APJRLN
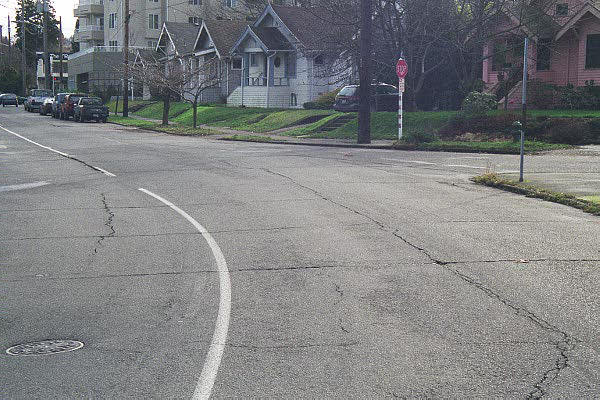
-
It is a type of crack that occurs in an asphalt overlay or surface treatment when it reflects or mimics the pattern of cracks, joints, or other discontinuities present in the underlying pavement structure.
-
Reflection cracks are commonly observed in the following situations:
-
Asphalt overlays on jointed concrete pavements: When an asphalt overlay is placed over an existing jointed concrete pavement, the joints in the concrete can eventually reflect through the asphalt layer, causing cracks to appear on the surface that mimic the pattern of the underlying concrete joints.
-
Asphalt overlays on cracked asphalt pavements: If an asphalt overlay is placed over an existing asphalt pavement that has developed cracks or other distresses, these underlying cracks can propagate upwards and reflect through the new overlay, forming similar cracking patterns on the surface.
-
Surface treatments on cracked pavements: In the case of surface treatments like chip seals or slurry seals applied to existing cracked pavements, the underlying cracks can reflect through the new surface treatment, causing similar cracks to appear on the treated surface.
-
Reflection cracks are considered a structural distress and can compromise the integrity and performance of the pavement surface. They allow water infiltration, which can lead to further deterioration of the pavement structure, such as base or subgrade failure, potholes, or additional cracking.
-
In PMS, reflection cracks are typically identified, mapped, and rated based on their severity (width, density, and pattern) and extent (percentage of the pavement area affected). Depending on the level of distress, maintenance or rehabilitation strategies may include crack sealing, patching, or more extensive treatments like milling and overlaying or full-depth pavement replacement.
-
Proper evaluation and timely maintenance of reflection cracks are essential to prevent further deterioration and extend the service life of the pavement.
Corner Break
Related code(s): CPCBLN
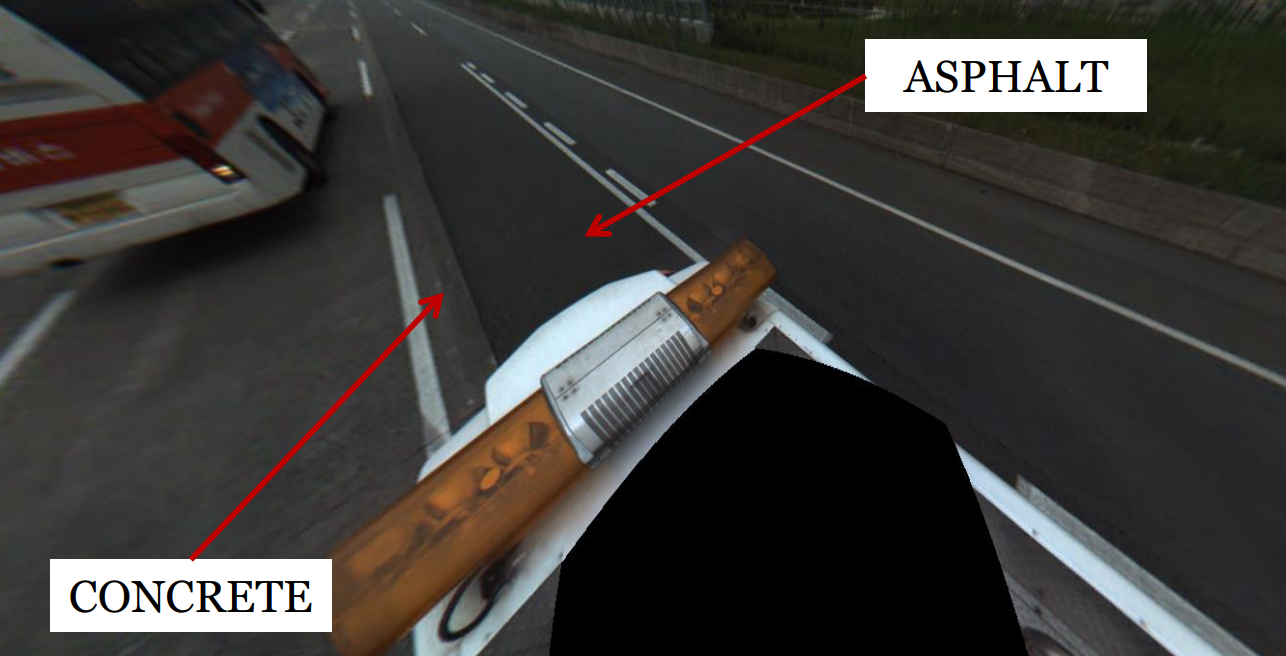
-
Corner Break means a junction line when two pavement types are existing in full longitudinal(vertical) length. This is different from patch but when the vertical length of a patch is longer than image size, it could be understood as Courner Break.
-
In this case, one 10m long image file can have both concrete and asphalt crack codes.
Asphalt Patch
Related code(s): APPAAR, CPPAAR
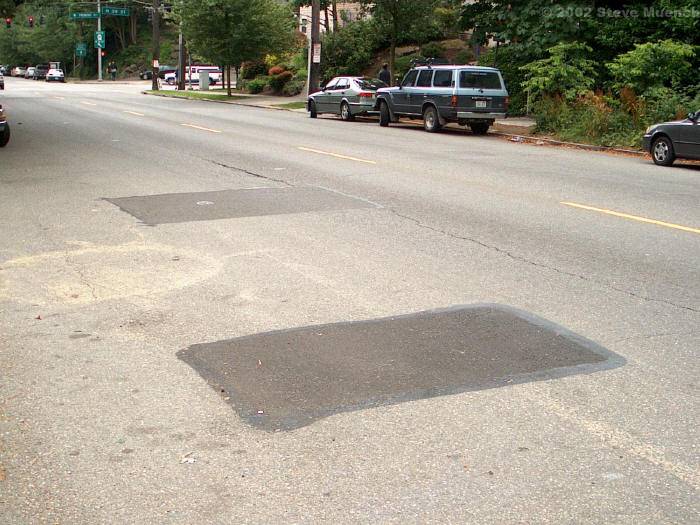
-
It refers to a localized repair or replacement of a portion of the asphalt pavement surface that has been damaged or deteriorated.
-
Asphalt patches are commonly used to address various types of distresses in asphalt pavements, such as potholes, alligator cracking, rutting, or utility cuts. The patching process involves removing the damaged or deteriorated asphalt material and replacing it with new asphalt mix.
-
In PMS, asphalt patches are typically identified, recorded, and evaluated based on several factors:
-
Size: The area or dimensions of the patch are measured and recorded.
-
Condition: The condition of the patch is assessed, considering factors like cracking, raveling, or deformations within the patch itself.
-
Age: The age or approximate time since the patch was installed may be recorded, as older patches may be more prone to deterioration.
-
Ride quality: The ride quality or smoothness over the patch area is evaluated, as patches can sometimes create bumps or irregularities in the pavement surface.
-
Distress type: The type of distress that led to the need for patching is often recorded, as this can provide insights into the underlying causes and potential for future deterioration.
-
In PMS, asphalt patches are generally considered a temporary or localized repair measure. While they can extend the serviceability of the pavement in the short term, they may not fully address the underlying causes of the distress. Depending on the extent and severity of the patching, as well as the overall condition of the pavement, more comprehensive rehabilitation or reconstruction strategies may be recommended by the PMS.
-
Regular monitoring and evaluation of asphalt patches are essential to ensure their performance and to identify any potential issues or the need for more permanent repairs or rehabilitation.
Concrete Patch
Related code(s): CPPPAR
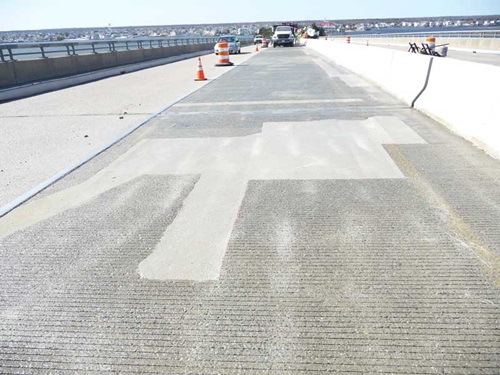
-
It refers to a localized repair or replacement of a portion of a concrete pavement surface that has been damaged or deteriorated.
-
Concrete patches are commonly used to address various types of distresses in concrete pavements, such as spalling, cracking, joint failures, or localized deterioration due to factors like heavy traffic loads, environmental conditions, or material defects.
-
In PMS, concrete patches are typically identified, recorded, and evaluated based on several factors:
-
Size: The area or dimensions of the patch are measured and recorded.
-
Condition: The condition of the patch is assessed, considering factors like cracking, spalling, faulting, or material degradation within the patch itself.
-
Age: The age or approximate time since the patch was installed may be recorded, as older patches may be more prone to deterioration.
-
Ride quality: The ride quality or smoothness over the patch area is evaluated, as patches can sometimes create bumps or irregularities in the pavement surface.
-
Distress type: The type of distress that led to the need for patching is often recorded, as this can provide insights into the underlying causes and potential for future deterioration.
-
In PMS, concrete patches are generally considered a temporary or localized repair measure. While they can extend the serviceability of the pavement in the short term, they may not fully address the underlying causes of the distress. Depending on the extent and severity of the patching, as well as the overall condition of the pavement, more comprehensive rehabilitation or reconstruction strategies may be recommended by the PMS.
-
Regular monitoring and evaluation of concrete patches are essential to ensure their performance and to identify any potential issues or the need for more permanent repairs or rehabilitation. Proper installation techniques, including adequate dowel or tie bar placement, and the use of high-quality patching materials, are crucial for the long-term performance of concrete patches.
Joint
Related code(s): CPF1LN, CPF2LN, CPF3LN
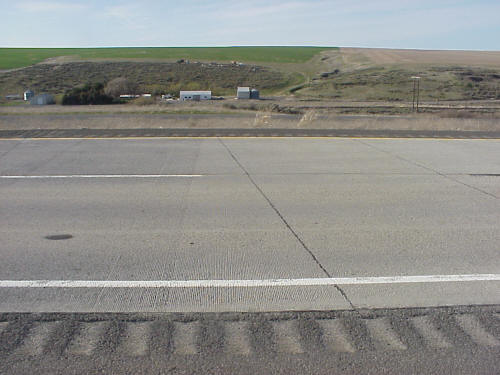
-
It refers to a planned discontinuity or separation in a concrete pavement surface that is designed to control cracking and accommodate movements caused by temperature changes, moisture variations, and applied loads.
-
Joints are intentionally constructed in concrete pavements to prevent uncontrolled cracking due to the inherent properties of concrete, such as its low tensile strength and tendency to shrink during curing and drying. Proper joint design and construction are crucial for the long-term performance and serviceability of concrete pavements.
-
In PMS, different types of joints are typically identified, evaluated, and monitored:
-
Transverse joints: These joints run perpendicular to the pavement's centerline and are spaced at regular intervals to control transverse cracking due to contraction and expansion of the concrete.
-
Longitudinal joints: These joints run parallel to the pavement's centerline and are used to separate lanes or accommodate wider pavement sections by dividing them into smaller lane-width slabs.
-
Construction joints: These joints are formed when concrete is placed in separate operations, allowing for the continuation of concrete placement while creating a planned joint between the two placements.
-
Isolation or expansion joints: These joints are designed to separate the concrete pavement from fixed structures, such as bridges or buildings, allowing for movement and preventing damage due to expansion or contraction.
-
In PMS, the condition of joints is typically evaluated based on factors such as:
-
Joint sealant condition: The condition of the sealant material within the joint is assessed for cracking, spalling, or loss of adhesion, which can lead to water infiltration and subsequent pavement deterioration.
-
Faulting or stepping: Vertical displacement or misalignment between adjacent slabs at the joint is measured, as it can affect ride quality and lead to further deterioration.
-
Spalling: The breakdown or dislodgement of concrete material along the joint edges is evaluated, as it can indicate poor load transfer or excessive stress concentrations.
-
Proper joint design, construction, and maintenance are crucial for the long-term performance of concrete pavements. In PMS, joint deficiencies are identified, and appropriate maintenance or rehabilitation strategies, such as joint resealing, load transfer restoration, or slab replacement, are recommended based on the severity and extent of the distresses observed.
Spalling
Related code(s): CPJ1AR, CPJ2AR, CPJ3AR, CPJ4AR
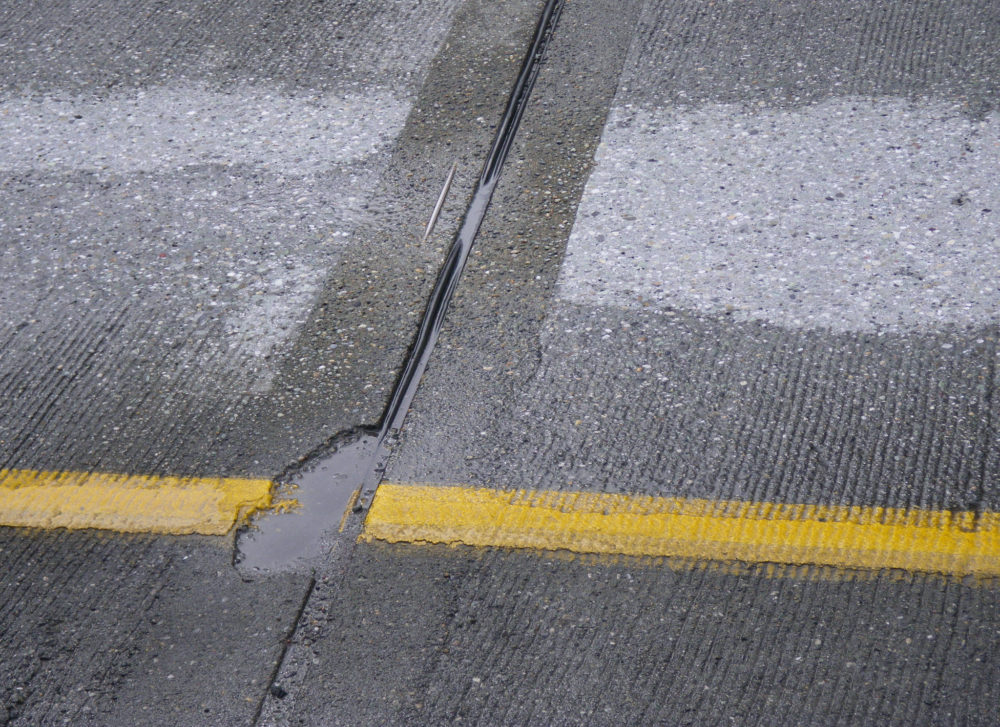
-
It refers to the cracking, breaking, or dislodging of small or large pieces of pavement material from the surface or edges of a concrete or asphalt pavement.
-
Spalling can occur in both concrete and asphalt pavements and is typically caused by a combination of factors, including:
-
Weathering and environmental effects: Repeated cycles of freezing and thawing, water infiltration, and exposure to deicing chemicals can cause the pavement material to deteriorate and spall.
-
Traffic loads: Heavy or repeated traffic loads can induce stresses and fatigue in the pavement material, leading to the breaking or cracking of the surface and eventual spalling.
-
Material deficiencies: Poor quality or improper curing of the concrete or asphalt mix can make the pavement more susceptible to spalling over time.
-
Reinforcement corrosion: In reinforced concrete pavements, the corrosion of reinforcing steel can cause expansive forces that lead to cracking and spalling of the concrete cover.
-
In PMS, spalling is typically identified, recorded, and evaluated based on several factors:
-
Severity: The depth, area, or volume of material lost due to spalling is measured and classified as low, moderate, or high severity.
-
Location: Spalling can occur on the pavement surface, along joints or cracks, or at the edges or corners of the pavement, which can have different implications for maintenance and repair strategies.
-
Extent: The percentage or total area of the pavement affected by spalling is quantified to assess the overall severity of the distress.
-
Spalling can compromise the structural integrity, ride quality, and serviceability of the pavement. In PMS, spalling is considered a distress that requires maintenance or rehabilitation, depending on its severity and extent. Maintenance strategies may include patching, crack sealing, or surface treatments, while more extensive rehabilitation may involve partial or full-depth pavement repairs or overlays.
-
Regular monitoring and timely repair of spalling are essential to prevent further deterioration and extend the service life of the pavement.
Expansion Joint
Related code(s): XPAJAR
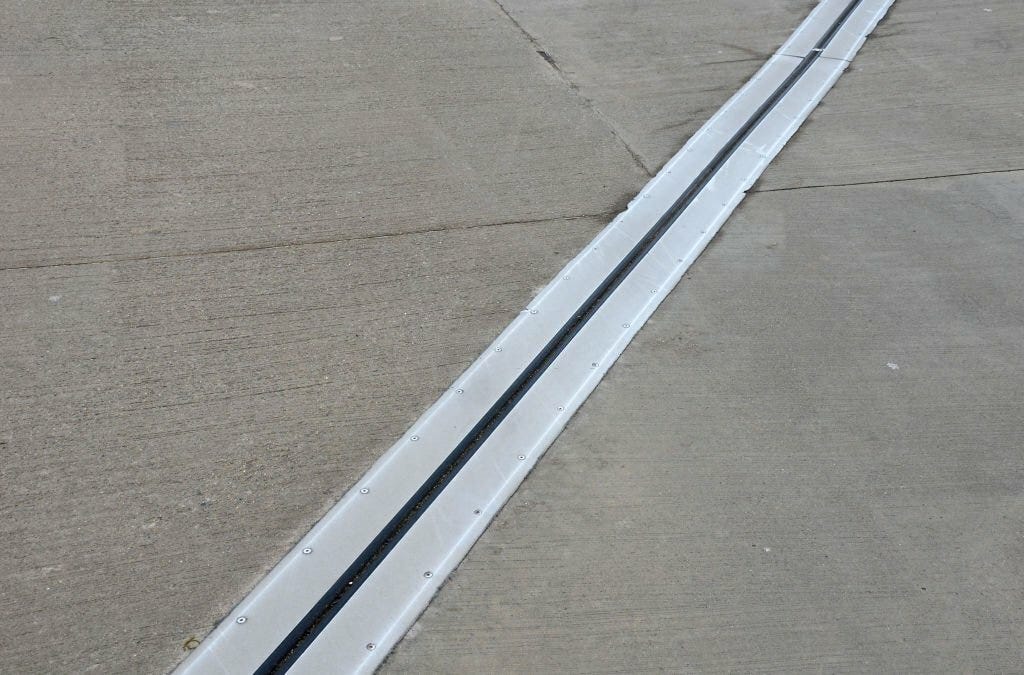
-
It is a specific type of joint intentionally constructed in concrete pavements to allow for the expansion and contraction of the concrete slabs due to temperature changes and other environmental factors.
-
Expansion joints are designed to accommodate the dimensional changes that occur in concrete pavement slabs, preventing excessive compressive stresses and potential buckling or blowups. These joints are typically wider than contraction joints and often include a compressible filler material, such as asphalt, rubber, or cork, to allow for slab movement.
-
In PMS, expansion joints are commonly found in the following locations:
-
At intersections or intersections with other pavements or structures: Expansion joints are used to separate the concrete pavement from adjacent structures, such as bridges, buildings, or other pavements, to prevent damage due to differential movement.
-
At regular intervals along long, continuous pavement sections: Expansion joints are spaced at specific intervals (typically 200 to 500 feet or 60 to 150 meters) to accommodate the overall expansion and contraction of the pavement.
-
At points of geometric changes: Expansion joints may be used at locations where the pavement geometry changes, such as curves or transitions in width, to accommodate potential movements.
-
In PMS, the condition of expansion joints is typically evaluated based on several factors:
-
Joint sealant condition: The condition of the sealant material within the joint is assessed for cracking, spalling, or loss of adhesion, which can lead to water infiltration and subsequent pavement deterioration.
-
Joint width: The width of the expansion joint is measured to ensure it is within the designed limits, allowing for proper slab movement without excessive opening or closing.
-
Faulting or stepping: Vertical displacement or misalignment between adjacent slabs at the joint is measured, as it can affect ride quality and lead to further deterioration.
-
Spalling: The breakdown or dislodgement of concrete material along the joint edges is evaluated, as it can indicate poor load transfer or excessive stress concentrations.
-
Proper design, construction, and maintenance of expansion joints are crucial for the long-term performance of concrete pavements. In PMS, deficiencies in expansion joints are identified, and appropriate maintenance or rehabilitation strategies, such as joint resealing, slab replacement, or load transfer restoration, are recommended based on the severity and extent of the distresses observed.
Edge Break
Related code(s): APECLN
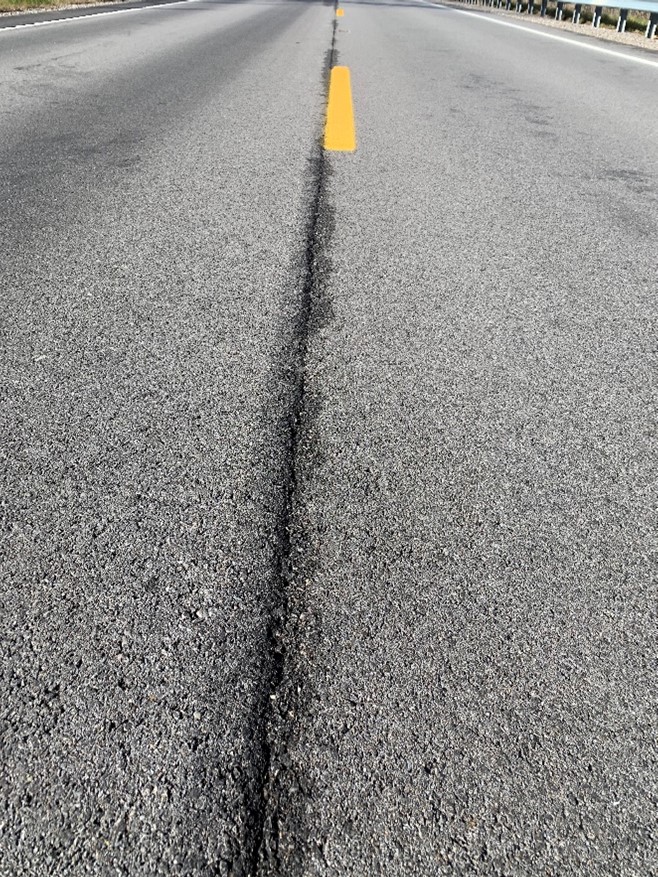
-
Edge Break crack refers to a longitudinal separation that occurs along the joint between asphalt lanes, typically arising in areas where the lanes were constructed at different times.
-
These cracks are usually caused by insufficient compaction of the mixture when paving adjacent to an existing pavement, leading to reduced density and accelerated oxidation of the asphalt, resulting in aggregate dislodgement. They can also occur if the paving temperature, aggregate segregation management, or subgrade stability were not properly controlled during construction.
-
If cracks have developed, crack sealing repair methods are used. If there is a significant height difference or potholes have formed along the cracked area, a partial depth repair is performed by removing only the surface layer and filling it with new material.
Edge Crack
Related code(s): N/A
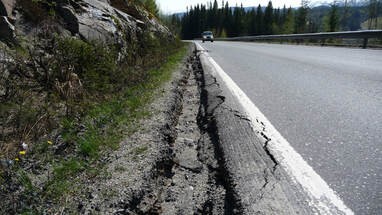
-
It refers to a crack that occurs along the edge or outer periphery of a pavement surface, typically within 1 to 2 feet (0.3 to 0.6 meters) from the edge.
-
Edge cracks are commonly found in both asphalt and concrete pavements and can be caused by various factors:
-
Lack of lateral support: Pavements require proper lateral support from the shoulder or adjacent materials to resist the stresses induced by traffic loads. If this support is inadequate or deteriorates over time, it can lead to the development of edge cracks.
-
Soil movement: Differential settlement or erosion of the underlying soil or base material near the pavement edge can cause the edge to lose support, resulting in cracking.
-
Moisture infiltration: Water can penetrate the pavement structure through cracks or joints and cause erosion or weakening of the base or subgrade materials near the edge, leading to edge cracking.
-
Thermal stresses: Temperature fluctuations can cause the pavement material to expand and contract, leading to stresses that may manifest as edge cracks, especially if the pavement is not properly tied to the adjacent shoulder or curb.
-
Edge cracks can be classified as longitudinal or transverse depending on their orientation along or across the pavement edge, respectively.
-
In PMS, edge cracks are typically identified and rated based on their severity, extent, and potential for further deterioration. Severe edge cracks can allow water infiltration, leading to additional distresses such as pumping, faulting, or base/subgrade failure.
-
Maintenance and repair strategies for edge cracks may include crack sealing, patching, shoulder repair or reconstruction, or even partial or full-depth pavement repairs, depending on the extent and severity of the distress. Addressing edge cracks is important to prevent further deterioration and maintain the structural integrity of the pavement.
Sealant Failure
Related code(s): N/A
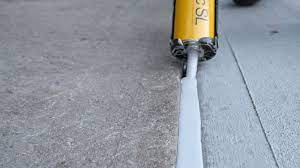
-
It refers to the material used to fill and seal joints or cracks in concrete and asphalt pavements.
-
The primary function of sealants in PMS is to prevent water and incompressible materials from entering the pavement structure through joints or cracks, which can lead to further deterioration and damage. Sealants also help in reducing the infiltration of damaging solutions, such as deicing chemicals, and can provide some load transfer capability across joints or cracks.
-
Common types of sealants used in PMS include:
-
Hot-poured sealants: These are thermoplastic materials, typically based on rubberized asphalt or other bituminous materials, that are heated and poured into the joints or cracks in a molten state. They are widely used for sealing joints in concrete pavements.
-
Cold-poured sealants: These are single or multi-component materials, often based on silicone, polyurethane, or other polymers, that can be applied at ambient temperatures. They are commonly used for sealing cracks in asphalt pavements and may also be used in concrete pavements.
-
Compression sealants: These are preformed, compressible materials, such as rubber, cork, or fiber-reinforced materials, that are inserted into joints to accommodate movement and prevent the ingress of water and debris.
-
In PMS, the condition of sealants is typically evaluated based on factors such as:
-
Adhesion: The degree of bonding between the sealant and the pavement surface is assessed, as poor adhesion can lead to water infiltration and sealant failure.
-
Cohesion: The internal integrity and consistency of the sealant material are evaluated, as degradation or loss of cohesion can compromise its sealing ability.
-
Spalling or cracking: Any cracking, splitting, or dislodgement of the sealant material within the joint or crack is noted and evaluated.
-
Overband or underband: The presence of excess sealant material on the pavement surface (overband) or insufficient sealant depth (underband) is assessed, as these conditions can affect the sealant's performance.
-
Regular inspection and maintenance of sealants are essential in PMS to ensure their effectiveness in protecting the pavement structure from water infiltration and subsequent deterioration. Timely resealing or replacement of failed or deteriorated sealants is a common maintenance activity to extend the service life of pavements
Block Cracking(BC)
Related code(s): N/A
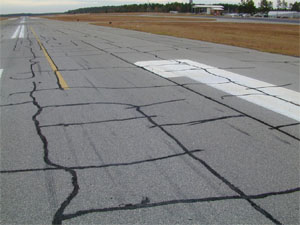
Edge Cracking(EC)
Related code(s): N/A

-
Asphalt edge cracking refers to those cracks that start on the side of the road and then spread toward the centre over time.
-
They pose a very big safety hazard for vehicles, which is why asphalt crack repairs should be administered as soon as possible.
Lane/Shoulder Drop-off (LDO)
Related code(s): N/A
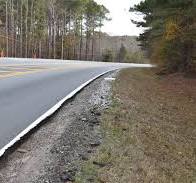
Diagonal Cracking (DC)
Related code(s): N/A

Ravelling/Weathering(RAV)
Related code(s): N/A
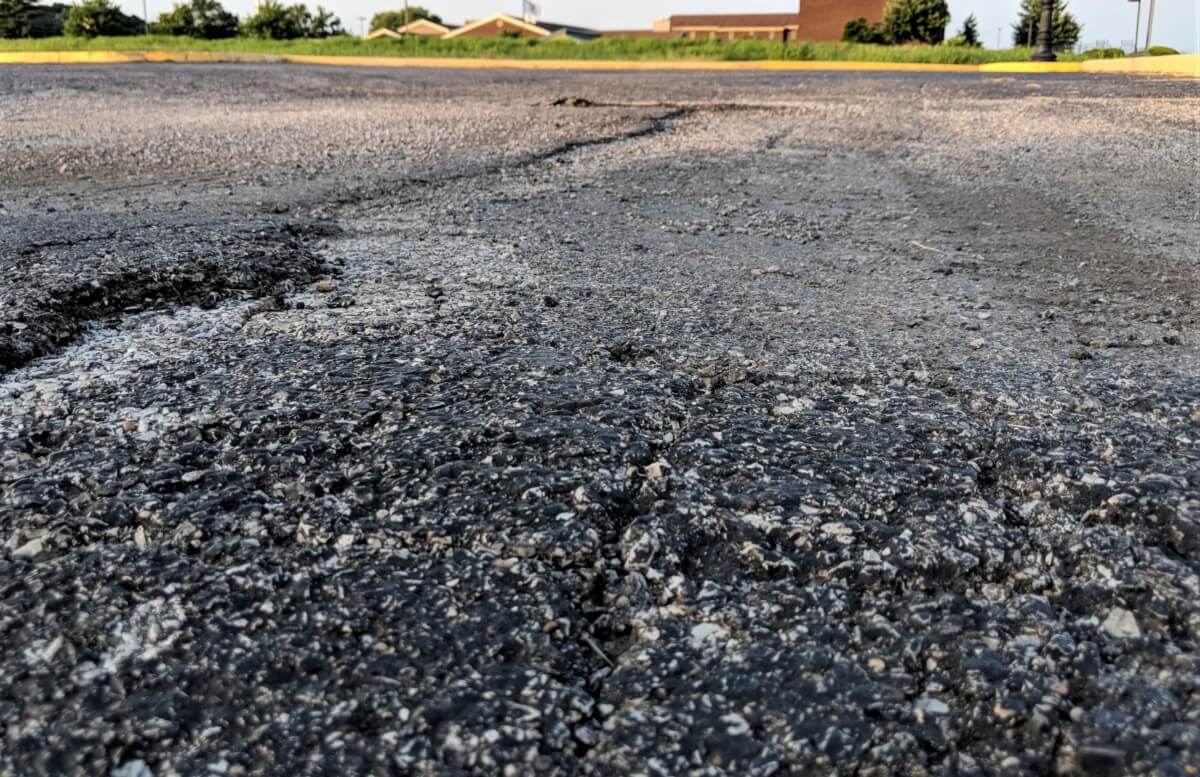
-
Raveling is the disintegration of an asphalt road surface. It is due to the dislodgment of the aggregate materials (gravel, sand, and crushed stone). It reduces skid resistance, roughens the road surface, and exposes the layers underneath to further deterioration.
Rutting(RUT)
Related code(s): N/A
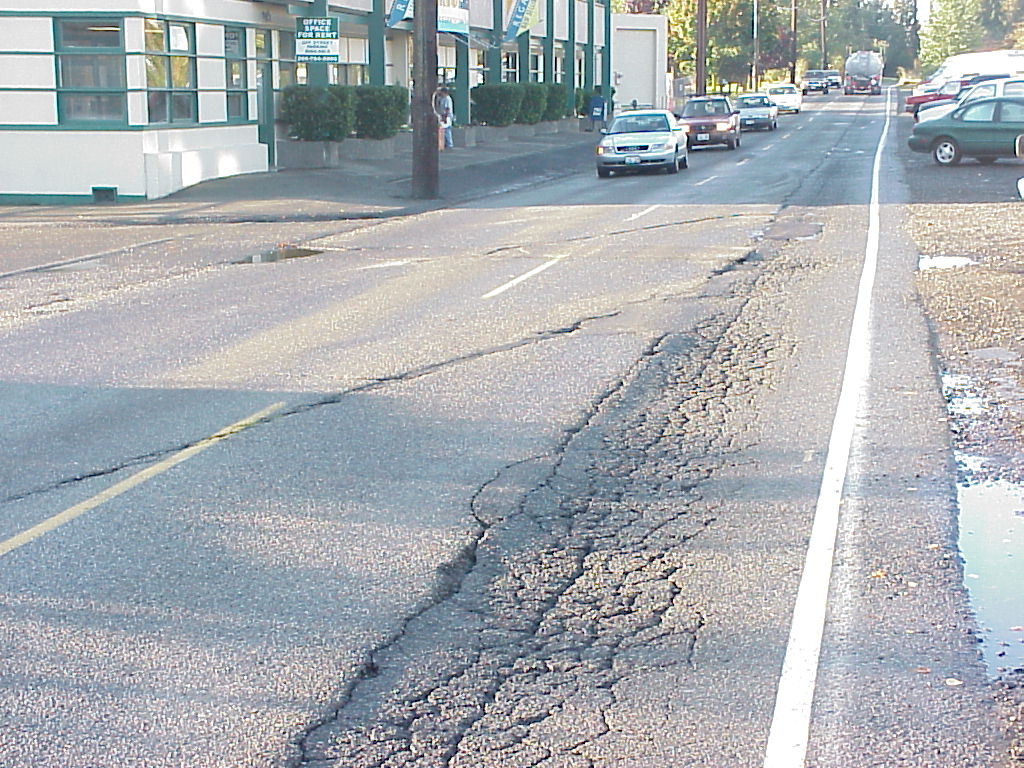
Shoving/Slippage(SHO)
Related code(s): N/A

Polished Aggregate(POL)
Related code(s): N/A

-
Repeated traffic applications. Generally, as a pavement ages the protruding rough, angular particles become polished. This can occur quicker if the aggregate is susceptible to abrasion or subject to excessive studded tire wear.
Potholes(POT)
Related code(s): N/A

-
Generally, potholes are the end result of fatigue cracking. As alligator cracking becomes severe, the interconnected cracks create small chunks of pavement, which can be dislodged as vehicles drive over them. The remaining hole after the pavement chunk is dislodged is called a pothole.
Pumping/Mud Jacking(PUM)
Related code(s): N/A

-
Pumping is the ejection of material by water through joints or cracks, caused by deflection of the slab under passing loads. As water is ejected, it carries particles of gravel, sand, clay, or silt, resulting in a progressive loss of pavement support.
Bleeding(BLD)
Related code(s): N/A
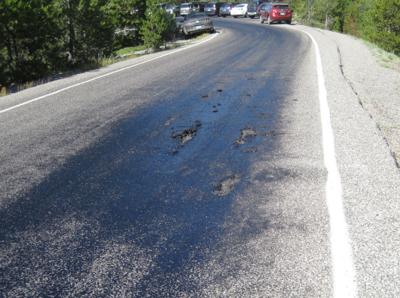
-
Bleeding is a film of bituminous material on the pavement surface that creates a shiny, glass like, reflecting surface that usually becomes quite sticky. Bleeding is caused by excessive amounts of asphaltic cement or tars in the mix, or low air void content, or both.